Used Rubber Machines With Tractor Tyre Manufacturing Process
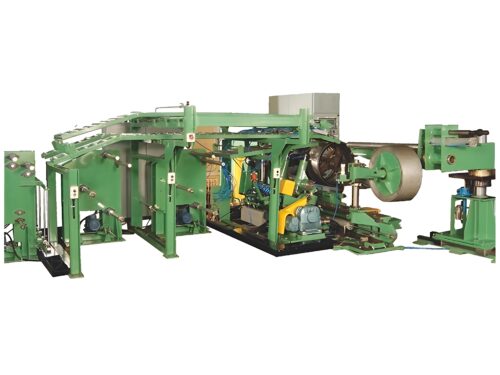
The rubber industry plays a pivotal role in various sectors, from automotive to construction. Within this expansive domain, tractor tire manufacturing stands out as a critical niche, supporting agricultural endeavors worldwide. However, the manufacturing process demands precision, efficiency, and advanced machinery. In recent years, the utilization of used rubber machines has gained momentum, offering cost-effective solutions without compromising quality. Let’s delve into the intricacies of tractor tire manufacturing and explore the integration of used rubber machines in this process.
Understanding Tractor Tyre Manufacturing –
Manufacturers make tractor tires to handle rough terrains, heavy loads, and extreme conditions. These are the conditions found in farming. The manufacturing process has many stages. Each stage is crucial for making durable and reliable tires.
1. Raw Material Preparation:
- Natural rubber, synthetic rubber, carbon black, oils, and various chemicals constitute the primary raw materials.
- These materials undergo thorough testing and processing to ensure consistency and quality.
2. Mixing:
- In this stage, the raw materials are blended using specialized machinery to create a homogeneous rubber compound.
- Precise mixing parameters are crucial to achieve desired characteristics such as strength, flexibility, and wear resistance.
3. Tire Building:
- The mixed rubber compound is then applied to tire-building machines, where it’s shaped into the desired tread pattern and dimensions.
- Multiple layers of rubber, fabric, and steel cords are strategically arranged to reinforce the tyre structure.
4. Curing:
- Curing involves subjecting the assembled tire to heat and pressure within a curing press.
- This process promotes cross-linking of rubber molecules, resulting in the final hardened and durable product.
Integration of Used Rubber Machines –
While the demand for advanced machinery in tire manufacturing is undeniable, the high costs associated with new equipment can pose challenges, especially for smaller manufacturers or those in emerging markets. This is where used rubber machines offer a viable alternative.
1. Cost Efficiency:
- Investing in used rubber machines significantly reduces upfront capital expenditure.
- Manufacturers can acquire high-quality machinery at a fraction of the cost of new equipment, enabling cost savings without compromising productivity or quality.
2. Sustainability:
- Opting for used machinery promotes sustainability by extending the lifespan of existing equipment.
- It reduces the environmental impact associated with manufacturing new machines and facilitates the reuse of resources.
3. Customization and Upgradation:
- Many used rubber machines can be customized and upgraded to meet specific manufacturing requirements.
- Manufacturers have the flexibility to integrate additional features or technologies as needed, enhancing operational efficiency and product quality.
4. Technical Support and Maintenance:
- Reputable suppliers of used rubber machines offer comprehensive technical support and maintenance services.
- This ensures optimal performance, minimizes downtime, and prolongs the operational lifespan of the equipment.
Conclusion –
Making tractor tires shows the complex processes. It also shows the advanced tech in the rubber industry. They move it forward. New machinery is a cornerstone of innovation and efficiency. But, integrating used rubber machines is a pragmatic approach. It’s for manufacturers seeking cost-effective solutions. By using used equipment, manufacturers can navigate economic challenges. They can also make sustainability better. They can maintain the rubber industry’s high quality.