Rubber Hot Feed Extruder: A Comprehensive Guide
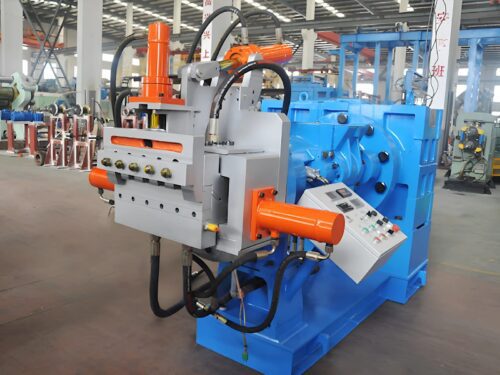
Rubber processing is one of the most critical stages in industries ranging from automobiles and space industries to making shoes and medical products. Among various equipment used in such processing, the rubber hot feed extruder stands out as vital and indispensable.Â
What is a Rubber Hot Feed Extruder?
The rubber hot feed extruder shapes and molds raw rubber material into the desired profiles. As a preheated rubber working unit, it ensures that the entire extrusion process runs smoothly and efficiently. Here, the machine will force the heated rubber out through the die, which will give it a particular shape, and the extruded shapes can be from simple tubing and seals to the more complex hoses or window gaskets.
Unlike a cold extruder, which feeds at room temperature, an extruder requires the rubber to be preheated. While this difference in operation does indeed allow for quicker processing and is ideal for those applications requiring high output and fast speed, its dual-feeding system with its surrounding screens enables it to process material continuously without stopping.
How Does a Rubber Hot Feed Extruder Work?
The rubber hot feed extruder works through several key steps:
Pre-heating of Rubber: At this stage, the process heats the rubber compound to a specific temperature, making it soft and workable.
Feeding into the Extruder: The pre-heated rubber is then fed into the extruder barrel. The screw, by rotating, pushes the rubber forward.
Compression and Shaping: The compression of the rubber occurs while it passes through the extruder. The pressure increases as it is forced into shape coming out of the die.
Cooling and Cutting: As the rubber now comes out in the shape desired, cooling occurs and may also be cut to the appropriate length if needed.
It produces solid, continuous rubber products, or specific-length parts. The speed and the ease of this process result in it being highly versatile for large-volume production.
Features of Rubber Hot Feed Extruders –
Pre-heating- The rubber must be pre-heated for the extruder to enable higher speed rates.
Custom Dies- This extruder is designed with custom-made dies to make a wide variety of shapes and profiles of parts according to a particular industry’s demand.
Versatility- It is used with several natural rubber, synthetic rubber, as well as silicone compound types.
High Output- Because it runs continuously, this type of hot feed extruder can deliver very large quantities of rubber extruded efficiently.
Applications of Rubber Hot Feed Extruders –
Rubber hot feed extruders have wide-ranging applications across a range of industries:
Automotive: The manufacturing of seals, gaskets, hoses, and other rubber components used in cars and trucks.
Construction: Creation of window and door seals, expansion joints, and rubber sheets.
Medical: Manufacturing medical tubing and other rubber products in the health care area.
Footwear: Rubber soles and other parts of footwear and boots are produced through the extrusion process.
Advantages of Using a Rubber Hot Feed Extruder –
Efficiency:Â The heated extrusion process boosts production rates by speeding up rubber entry into the machine.
Better Control Over Output: Manufacturers can regulate extrusion pressure and speed to ensure consistent product quality.
Cost-Effective for Large-Scale Production: Hot feed extruders excel in industries needing continuous rubber production, minimizing downtime and maximizing throughput.
Maintenance and Considerations –
The rubber hot feed extruders are rather robust and reliable, but regular maintenance is highly necessary for smooth running operations. One of these includes:
Checking Screw and Barrel Wear: The rotating screw and barrel may ultimately wear out owing to the rubber material’s constant friction. Regular checks with timely replacement would ensure it.
Temperature Control:Â Heat the rubber uniformly to ensure that the end product maintains consistent quality. The fundamental ability towards uniform temperature control will significantly contribute to uniform extrusion.
Die Cleaning and Care: Effective cleaning of the die following every production run will ensure that the next batch maintains its intended shape free from defects.
Conclusion –
A rubber hot feed extruder plays a crucial role in the rubber industry. It delivers high production speeds and adapts to a variety of applications. The machine can shape the rubber to the desired forms be it an automobile component or a medical device. Since the business machine needs to be in proper working condition to ensure the production of quality products on a large scale, investing in the proper maintenance techniques would hence facilitate its smooth running.
For More Information Visit HereÂ