What Is an Open Mixer (2-Roll Mill) and How Does It Work?
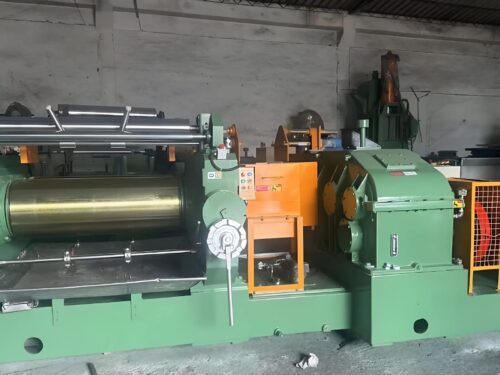
An open mixer, also referred to as a 2-roll mill, plays a crucial role in the rubber and plastics industries. This machine is widely used for blending, sheeting, and mixing raw materials efficiently. The role of this machine is to take part in processing raw materials in the early stages, thus making it easier to blend, soften, and prepare the material for use in subsequent production. It may be interesting to know how a 2-roll mill works for a first-time manufacturer or an industrious equipment hobbyist.
What is an Open Mixer (2-roll Mill)?
An open mixer features two large rollers, positioned horizontally in a cylindrical arrangement. These rollers, crafted from high-grade steel, rotate toward one another. The gap between the rollers is adjustable, allowing control over the material’s thickness. The rollers operate at different speeds to stretch and mix the material effectively.
These mills are referred to as “open” because the design exposes the material, making it visible to the operator. This openness enables manual adjustments and simplifies process monitoring.
How Does an Open Mixer Work?
The basic working principle of an open mixer is very simple. Here’s a step-by-step breakdown of how it works:
- Material feeding: The raw material, such as rubber, plastic, or any other compound, is fed to the gap between the two rollers. This can either be done manually or through a sophisticated system related to the specific setup of the mill.
- Rolling and Mixing: The material is drawn between rollers that rotate. As this is a rolling action, one of the rollers moves relatively more than the other roller; thus it causes shear forces. The process stretches the material, compresses it, and mixes it well. In the process, it ensures that the raw material is well distributed and softened.
- Adjusting the Gap: The operator can adjust the distance between the rollers to control the thickness of the material. A smaller gap creates a thinner sheet, while a wider gap allows for more thickness in the sheets of the material.
- Recycling the Material: Recycling the material through the rollers several times often achieves the desired consistency for the mixture, as the passes improve uniformity with each go.
- Final Product: After the material reaches the desired consistency and thickness, operators withdraw it from the mill and transfer it to a molding machine or an extruder for shaping in the rubber manufacturing process.
Key Features of a 2-Roll Mill
- Adjustable Gap: In any 2-roll mill, the adjustable gap is a feature that provides an assured level of control over the diameter of the material produced.
- Roll Speed Difference: Differential speed between two rollers in an open mixer enables shear action that mixes.
- Cooling or Heating Mechanism: Many open mixers actively utilize cooling or heating systems to regulate processing temperatures, ensuring the machine stays at an optimal level without overheating or cooling excessively.
Applications of Open Mixers (2-Roll Mills) –
- Rubber Mixing: A 2-roll mill is necessary for rubber products, such as tires, belts, and seals. The machine blends an additive, fillers, and raw rubber into a homogeneous mixture.
- Plastic Processing: Open mixers play an active role in plastic manufacturing by mixing polymers with additives, colorants, and stabilizers to produce plastic sheets, films, and other products.
- Material Testing: Research and development laboratories carry out small-scale testing on new materials and compounds using open mixers before their commercial production on a large scale.
Benefits of an Open Mixer –
- Versatility: A 2-roll mill can work on several materials, so it is a very versatile piece of equipment in manufacturing.
- Control: Gap size and speed control ensure accurate mixing and blending, crucial for material manufacturing.
- Easy to Use: The open design allows operators to view and adjust the process to ensure consistent results easily.
Safety Considerations –
Although open mixers may be efficient and widely used, it is still, on their side, necessary to have strict security measures. Open rollers, exposed to the environment, present a significant safety risk. Accidents can happen if proper protective gear is not used and standard operating procedures are ignored.
Conclusion –
An open mixer is essential for the rubber and plastics industries, saving time and boosting production by efficiently processing materials. Understanding its function helps appreciate the creation of items like tires and plastic films. For manufacturing, a quality 2-roll mill ensures smooth, high-quality products.
For More Information Visit Here