Vacuum Molding: Precision Solutions for Rubber and Plastic
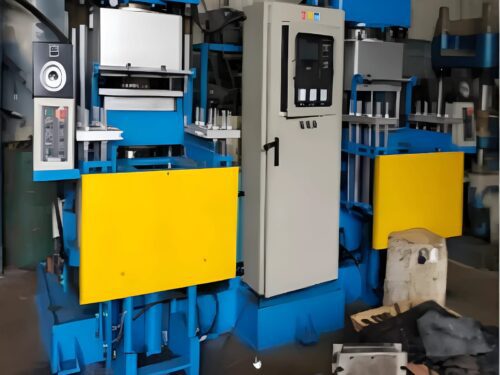
Precision and effectiveness are two of the most significant requirements in manufacturing. Vacuum moulding has served as a responsive alternative to producing good quality rubber and plastic products. This process ensures precision while having various benefits that make it applicable in different industries. Thus, what is vacuum moulding? How does it work? And what are its advantages in rubber and plastic production? Let’s discuss these questions below.
What is Vacuum Moulding?
Vacuum moulding is the process of manufacturing which applies vacuum pressure on rubber or plastic to give them any desired shape, and it is largely used in manufacturing where high tolerance products are designed having intricate designs. The process of creating a mould, heating the material to a point where it can be pulled into the mould by vacuum pressure, results in parts made with great precision and consistency.
How Does Vacuum Moulding Work?
The vacuum moulding process would work somewhat like this:
Creation of Mould: The first step would involve the creation of a mould, which could be either metal or silicone. It’s made according to the requirements of the product.
Preparation of Materials: Rubber or plastic sheets are prepared and heated up until they become softened and extremely flexible.
Vacuum Application: After preparation, the material is positioned on top of the mould. The product is next subjected to vacuum application. This application will stretch down the material into the mould. The material is guaranteed to adopt just the shape that has been designed in the cavity.
Cooling and then hardening: Following the adoption of the shape of the mould by the material, it is cooled down to allow it to harden. In this manner, the product is bound to maintain its shape and dimensions.
Demolding: The final product is now moulded and prepared for inspection and further processing if needed.
Advantages Vacuum Moulding –
Excellent Precision: Vacuum moulding can also produce very precise parts. The vacuum pressure eliminates all spaces within the mould and produces highly accurate products without having one flaw, letting every seam be perfectly smooth and ensuring exact dimensions.
cost-effective: This makes use of less energy compared to compression moulding, thus cutting down the costs of production.
Versatility: Vacuum moulding may often be quite cost-effective, particularly for small to medium volumes of production. It easily produces high-quality moulds that can be used to manufacture within a short time frame and thus less labour but waste of materials. In addition, the mould is reusable for several cycles of production, which further reduces costs.
Flexibility: It is versatile enough to accommodate a wide range of materials, including various types of rubber and plastics, to enable relatively easy production of a wide variety of products automotive parts and consumer goods to others. Because of this, manufacturers can easily switch between different materials as per the specific needs of a project.
Reduced Lead Time: The period or lead time for vacuum moulding is relatively short compared to the conventional method of moulding. As the moulds take a short time to prepare and also because of the efficiency of the vacuum application, the products will be taken to the market sooner. This speed is a very important factor that brings competitive businesses into the market.
Minimal Waste: The vacuum moulding process wastes very minimal amounts of material. This is because the material used is aptly utilised in making the final product. Apart from the environmental benefits, this process improves the general efficiency of production. Manufacturers can therefore choose sustainability while maintaining high-quality results.
Conclusion:
Vacuum moulding has always been a precise method for making rubber and plastic products, and the technique is very valued in the manufacturing industry. A distinction of vacuum moulding is its ability to make small intricate designs and cut down on production costs, minimising waste, which places it as an advantage for businesses which want to elevate their production processes. Whether one is working in the automotive industry or even doing product development for consumer goods, vacuum moulding can help one get precision and efficiency in producing with a view of succeeding in the business.
For More Information Visit Here