The Role of Rubber Calenders in Sheet Manufacturing
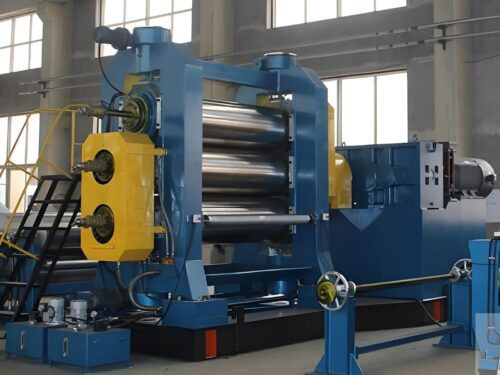
Rubber calendars are among the most significant manufacturing machines that produce quality rubber sheets. These are essential in a number of industries. The automobile and textile industry largely depends on the rubber sheet, so calendars are very important in fulfilling this demand. Thus, the blog will discuss what a rubber calendar is, how it works, and its importance in the process of rubber sheet manufacturing.
What are Rubber Calendars?
Heavy-duty, mechanically operated machines called rubber calenders constitute two or more large rolls of steel, aligned correctly to provide the needed thickness, texture, and finish on the sheets of rubber produced. Rubber fed in raw form to these rollers is flattened into sheet format with consistent thickness and other desired properties for smoothness.
The rubber calendar is an efficiency and precision-made machines that manufacture products that are accuracy and consistency-oriented. These machines can work on various types of rubber materials, including both natural and synthetic rubber, as well as rubber composites with added reinforcements like fabric layering.
Working on the Rubber Calenders –
This process uses the straightforward principle of calendering rubber by feeding raw rubber between a series of rollers that rotate toward each other. The rollers press and shape the material to achieve the desired uniformity. By adjusting the spaces between the rollers, operators can create even thin sheets with precise control over dimensions.
- Pre-rubber processing: The rubber is first mixed and softened. It thus becomes amenable to the calendering machine. Additives and reinforcement are added with raw rubber to achieve a given set of material properties.
- Feeding the Rubber Compound: The prepared compound is fed through the rollers in the calender. While moving through the rollers, it undergoes compression between them to yield a thin uniform sheet.
- Thickness and texture control: The rolls have adjustments to control the thickness and surface finish of the sheets. For example, in polished rolls, there are smooth surfaces; but there are textured rolls too with specific patterns on the sheets.
- Sheet collection: The collected sheets are either wound onto a spool or cut depending upon the use.
Different types of Rubber Calenders –
Many kinds of rubber calenders have various purposes in use. Such types of calendars are:
- Two-Roll Calendar: These are very useful in simpler applications and for creating uniform sheets.
- Three-Roll Calendar: To achieve a specific quality level in multi-layering a sheet, operators use a three-roller calendar, which enables precise control over layering measurements.
- Four-Roll Calendar: These provide control in an even higher range with the possibility of creating complex textures and efficiency in production.
Importance of Rubber Calenders in Sheet Manufacturing –
Rubber calendars are the ultimate performers that ensure consistency and quality being demanded by the industry. The following is why they are so precious in sheet manufacturing:
1. Accuracy and Consistency
Rubber calenders are precision devices. A millimeter control on thickness would ensure that every sheet coming out of the rubber calendar meets the specifications with precision. This is the case in applications such as automotive gaskets, industrial belts, and medical products, where variations in thickness can affect performance and safety.
2. Enhanced Production Efficiency
Rubber calenders streamline the manufacturing process with high processing speeds and minimal waste. Modern calendars are built with automation features, allowing for continuous, uninterrupted production. This becomes critical to satisfy large-scale demands without sacrificing quality.
3. Flexibility for Customization
Rubber calenders enable manufacturers to process a variety of materials and specifications to produce customized sheets for specific applications. One can have the ability, using a rubber calendar, to produce a smooth or textured sheet, thick or thin.
4. Cost Savings
With waste reduced and the opportunity to do large production runs, rubber calenders result in significant savings on cost. The processing control does not require a high degree of rework and will allow for more efficient production time and reduce overheads.
Applications of Calendered Rubber Sheets –
Calendered rubber sheets find applications in the following:
- Automobile Industry: Manufacturers use calendered rubber sheets to create seals, gaskets, and even tires.
- Textile Industry: Manufacturers apply calendered rubber sheets as a water-resistant coating on textiles.
- Health Industry: In sheet protection, padding, and other accessories used in medical equipment.
- Building Industry: Rubber sheets have applications in roofing, floor, and insulation purposes.
Conclusion –
Rubber calenders hold the heart of high-quality sheet manufacturing, allowing industries to produce durable, consistent, and reliable rubber sheets in all applications. Their accuracy, flexibility, and cost-effectiveness make them indispensable in today’s manufacturing. With advancements made in calender technology, the future promises even better efficiency and quality, solidifying rubber calenders more than ever as a bedrock of industrial production.
Investments in top-quality rubber calenders will provide great long-term benefits for manufacturers concerned with the quality and efficiency of production.
For More Information Visit Here