Rubber Injection Molding: A Comprehensive Guide for Beginners
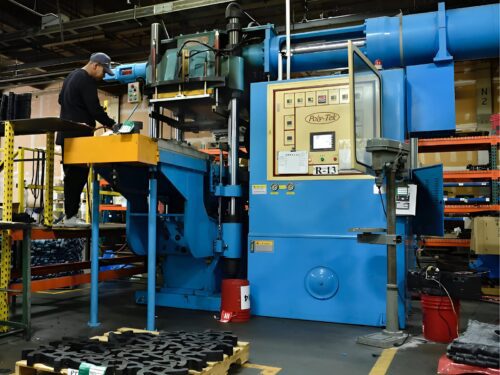
Among the widely used processes in manufacturing rubber parts and products, there is this very popularly known one called injection moulding of rubber. The process is efficient and of the level of precision with the possibility of manufacturing complex shapes in quality with minimum waste. Hence the requirement for such a process has been growing in several industries. We will break down the basics of rubber injection moulding, derive its benefits, and even give further details on applications in various industries in this blog post.
What is Rubber Injection Moulding?
Pre-molding uncured rubber and heating it under pressure were the early steps involved in the process of rubber injection moulding. Once inside the mould, the rubber cools and hardens, having assumed the shape taken by the mould. The method is generally suitable for producing parts ranging from simple O-rings and seals to complex parts, such as large automotive components.
Identified stages of the process include the following:
i) Rubber Compound Processing: The rubber compound is softened, so that it can flow without any inhibition.
ii) Injection: The molten rubber from the screw or piston injection injects into the mould.
iii) Moulding: The mould cavity of the rubber fills and takes its shape.
iv) Cooling: After filling the mould cavity, the mould cools down and gets the rubber hardened.
v) Ejection: The rubber part ejects from the mould after the cooling and hardening of the rubber.
Advantages of Rubber Injection Moulding-
There are many advantages that come with rubber injection moulding, hence why the technique comes as one of the favourites when it comes to production, and this lists some of those advantages.
- High Efficiency and Speed
Injection moulding is faster and more efficient than other methods of moulding. It can produce parts on a large scale with minimal interference from man once the mould is placed in position.
- Precision and Consistency
It will also be highly precise to ensure that the same components have minimal deviation. This is crucial for industries like the automobile and healthcare, where precision comes first.
- Complex Designs
Injection moulding can create designs which are too complicated and difficult or impossible by some other means. It’s suited for creating parts with detailed features or tight tolerance requirements.
- Waste Minimization
Because the rubber is injected directly into the mould cavity, less material waste is generated compared to other processes, such as compression moulding.
- Flexibility
Rubber injection moulding works with all kinds of rubbers: natural rubber, silicone, as well as synthetic rubbers like EPDM and nitrile. Thus, it is a flexible process for a wide number of industries.
Applications of Rubber Injection Molding-
Several industrial applications have adopted the technique of rubber injection moulding because it is flexible and reliable. Some of the common applications in which this technique can be made use of include the following:
- Automotive Industry
While producing seals, gaskets, and vibration-dampening components in the automobile industry, rubber injection moulding is utilised when parts have to undergo extreme conditions, for which rubber has been proven to be ideal.
- Medical and Healthcare
This process also produces other parts such as seals, grommets, and even custom medical grade. Since medical devices have high demands, using injection moulding is the best alternative because of integrity and accuracy.
- Aerospace
When applied to aerospace applications, the rubber parts would have to face extreme conditions. Injection moulding of rubber is also used in the manufacture of components, which comprise O-rings, seals, and gaskets that are deemed essential for giving strength and accuracy to parts in aerospace applications.
- Consumer Goods
The versatility of rubber injection moulding can produce high-grade end-products in quantity at relatively affordable costs-from the most mundane items of daily usage like rubber grips and appliance seals to other humble domestic items.
Key Requirements for Successful Rubber Injection Molding –
Rubber injection moulding is a process where several aspects need to be taken into account for optimum results:
- Material selection: Rubber may be different based upon the type. There are many types of rubber and they have different properties. Selection of this material may deteriorate if this is not selected according to requirement.
- Designing the Mould: The rubber mould has to be designed. The designing for the rubber mould must be with a consideration that must carry the properties of flow and cooling. Thus, proper designing of the mould minimises the defects, so high-quality parts can be produced.
- Temperature Control: It would require temperature to be maintained during the whole process to avoid defects such as air bubbles or improper curing.
Conclusion –
Rubber injection indeed is one of the most powerful and efficient processes for producing high-quality rubber parts. The versatility and precision of this process in addition to complexity in terms of shape all make it an excellent fit for various industries. Whether it’s an industry as huge as automotive markets, medical industry or just consumer goods, rubber injection moulding may very well deliver quality with performance.
For More Information Visit Here