The Impact of Automation in Rubber Processing Machines
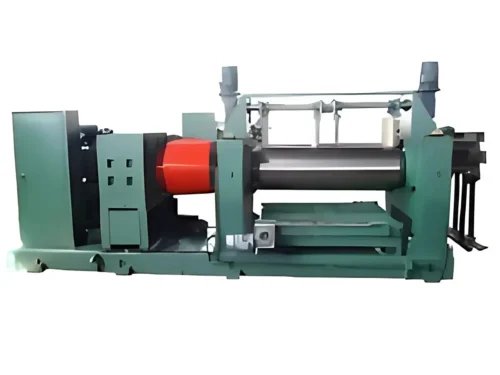
Over the past few years, automation has transformed so many industries. It’s not an exception to have changed the rubber processing industry. Automating rubber processing machines improved productivity, quality, and cost efficiency, thus turning the old manufacturing style into a modern, efficient industry.
1. Improved Efficiency and Productivity
Automation has significantly increased the speed and efficiency with which rubber processing machines carry out their operations. Automated systems execute repetitive tasks faster and more accurately than human labor; this reduces production time and increases output. Machines with automated controls can mix, mold, and cure rubber, reducing the chances of errors from human intervention. Because of this, manufacturers will be able to meet their higher demands without compromising the quality, especially in cases such as automotive, medical, and construction, as rubber products are very necessary.
2. Better Quality and Homogenization
In rubber processing, accurate control of temperature, pressure application, and timing must be ensured to reach the best quality. Machines are programmed to monitor these factors and adjust them in an accurate manner to deliver consistent quality in every product batch. This consistency may reduce variations and defects in rubber products, which may also improve their performance and durability. For manufacturers, such high-quality standards can win the trust of customers, thereby improving brand reputation, which leads to increased demand and market share.
3. Cost Cutting
There can be at least three derivations of the cost-benefit of automation in rubber processing. Firstly, mechanized machine uses far fewer human beings than human intervention; thus, it results in lower labor costs. Machines do not get tired quickly, so an extended operating period without frequent brakes or shift changes minimizes costs. Machines consume much lesser amounts of raw material because these are used efficiently, and as such, much lesser wastage, apart from lesser labor costs, keeping the cost of production very low to be competitive in the market.
4. Improvement in Workers’ Safety
Rubber processing is operations that expose personnel to dangers because of high temperatures, chemicals, and machinery. Automation prevents danger since human involvement in risky processes is minimized. For instance, machines that load, unload, and mix take care of dangerous tasks with workers at a distance. As a result, automation leads to an increase in productivity while improving a safe working environment thus reducing the chance of accidents and health hazards.
5. Better Process Control and Monitoring
The process of rubber processing, under automation, is directly monitored and controlled. Modern sensors, control systems, and data analytics enable the monitoring of temperature, pressure, and speed parameters during production processes. In case an abnormality arises, the system adjusts the settings or reports it to the operators so they do not cause any more issues. This means minimal downtime and less disruption in running processes, which translates into smoother operations and stable output.
6. Environmental Gains
Processing rubber produces the highest energies and waste volumes compared with other processing operations. Mechanical automation allows machines to complete the intended processes at the set ideal conditions. Energy is diminished with waste. Automation means there is improved emission regulation as well as resource regulation of a manufacturer, and the implication is that manufacturers shall be adopting environmentally friendly ways of producing. Thus, corporations conserve and save the environment but instead get fewer regulatory infringements and reduce their production expenses.
7. Data-Driven Insights
Automation in rubber processing generates valuable data on the production process, equipment performance, and quality of the final product. Such insights are used to make decisions for the improvement of processes. For instance, going by production data can pinpoint areas where the company can become more efficient or provide maintenance. This insight helps manufacturers enhance their lines, reduce downtime, and stay ahead of their competitors.
Challenges of Automation in Rubber Processing –
Although automation has several benefits, it still comes with its challenges. Automating rubber processing technology is costly because it needs significant investments in machinery and software and training for the employees. In addition, smaller companies may find it hard to afford the initial costs, but with time, automation pays for itself with long-term savings and increased productivity.
Conclusion –
Without a doubt, the automation of rubber processing machines has transformed the sector to become more efficient, cost-effective, and sustainable. With increased productivity, product quality, worker safety, and cost cutting, the automation of rubber manufacturing is leading change and setting up companies for long-term success. We will see greater innovations and advancements in automation and will benefit from them more if technology keeps advancing.
Automation is no longer a luxury for big multinationals; it’s a requirement for business organizations to keep in touch with the trends nowadays. Introducing automation for rubber processing is not merely a modernization step but a strategic move that will put the business group on the growth and success path in an always-shifting industrial environment.
For More Information Visit Here