Used Hot Feed Rubber Extruder With Feed Roll Device
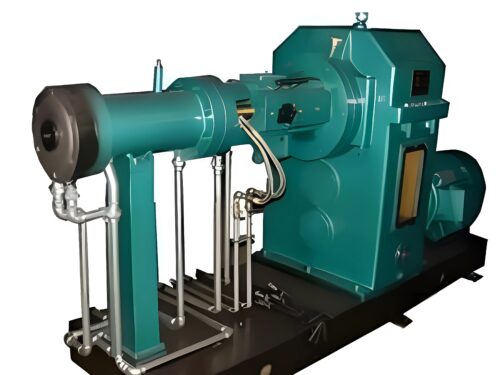
In the world of rubber processing, efficiency, precision, and cost-effectiveness are paramount. One of the key pieces of machinery in this industry is the hot feed rubber extruder, a device that plays a crucial role in shaping and forming rubber compounds. For businesses looking to enhance their production capabilities without breaking the bank, investing in a used hot feed rubber extruder with a feed roll device can be a game-changer. This blog will delve into the benefits and considerations of purchasing and using such equipment.
Understanding the Hot Feed Rubber Extruder –
A hot-fed rubber extruder is a machine designed to process rubber compounds by heating and forcing them through a die to create specific shapes and profiles. This type of extruder is particularly useful for continuous production processes, making it ideal for manufacturing rubber products such as tubing, seals, and profiles.
Key Components of a Hot Feed Rubber Extruder –
- Barrel and Screw: The core components where the rubber is heated and forced through.
- Die The part of the machine that shapes the rubber as it exits the extruder.
- Feed Roll Device: A critical addition that helps in feeding the rubber into the extruder consistently and efficiently.
Advantages of a Used Hot Feed Rubber Extruder –
1. Cost Savings: One of the most significant benefits of purchasing a used hot feed rubber extruder is the cost savings. New machinery can be prohibitively expensive, especially for small to medium-sized enterprises. By opting for a used model, businesses can save a substantial amount of money, allowing them to allocate funds to other areas of their operations.
2. Proven Performance – Used machinery often comes with a track record of performance. When buying from reputable dealers or previous owners, you can obtain maintenance records and operational histories that provide insight into the machine’s reliability and efficiency. This historical data can be invaluable in making an informed purchase decision.
3. Faster ROI – With lower initial investment costs, the return on investment (ROI) for a used hot-fed rubber extruder can be achieved more quickly compared to new equipment. This quicker ROI can help businesses reinvest in other areas, spurring further growth and development.
4. Sustainability – Purchasing used equipment is an environmentally friendly choice. By reusing machinery, you contribute to reducing the demand for new manufacturing and the associated environmental impact. This sustainable approach can also enhance your company’s image and appeal to eco-conscious customers.
Importance of the Feed Roll Device –
The feed roll device in a hot feed rubber extruder plays a crucial role in ensuring the efficiency and consistency of the rubber feeding process. Here are some key benefits:
1. Enhanced Consistency – The feed roll device helps maintain a consistent feed of rubber into the extruder, which is essential for producing uniform products. This consistency is particularly important for applications requiring precise dimensions and properties.
2. Improved Efficiency – By automating the feeding process, the feed roll device reduces the need for manual intervention, leading to improved efficiency and productivity. This automation minimizes downtime and maximizes output.
3. Reduced Material Waste – With consistent feed, there is less likelihood of material wastage due to overfeeding or underfeeding. This efficiency not only saves costs but also aligns with sustainability goals by minimizing waste.
Considerations When Buying Used Equipment –
1. Source and Reputation – Ensure you purchase from a reputable dealer or previous owner. Check for reviews, ask for references, and verify the credibility of the seller. A trustworthy source can provide detailed information about the machine’s condition and history.
2. Inspection and Testing – Before finalizing the purchase, conduct a thorough inspection of the extruder and feed roll device. If possible, witness the machine in operation to ensure it meets your requirements and performs as expected.
3. Maintenance Records – Request maintenance records and operational history. This documentation can give you insights into the machine’s reliability and any potential issues that may need addressing.
4. Compatibility and Upgrades – Ensure the used extruder is compatible with your existing setup and meets your production needs. Additionally, check if there are available upgrades or parts for future improvements or repairs.
For more information Visit Here